Additive Manufacturing
Metal 3D Printing
PureForm Technology
PureForm delivers complex, precision metal parts when you need them.
The method involves a unique mixture of MIM powder and a photoresistive polymer binder. Components are constructed layer by layer using specialized high-resolution, high-throughput optical printers. The subsequent “green state” components are then processed through debind and sinter, yielding parts that comply with MPIF-35 standards.
The backend process is virtually identical to MIM.
PureForm creates three significant advantages:
- Parts are quickly produced through printing, bypassing the time-consuming process of mold construction.
- Printed components exhibit a surface finish and feature resolution that exceed the capabilities of other additive manufacturing technologies.
- PureForm components can be scaled quickly and economically to facilitate low-volume production and ease the transition to Metal Injection Molding (MIM).
Prototyping and Low-Volume Production
GGI’s PureForm technology provides complex, precision metal parts for rapid prototyping, production, and replacement parts.
The PureForm platform achieves features as fine as 50 microns with 100-micron walls, meeting MPIF-35 standards, and prints parts that were previously only possible with approaches that have longer lead times and are more difficult to iterate.
Production-Ready Printing
Applications to date have included:
- Robotic Assited Surgery (RAS) instruments
- Surgical tool R&D and product development
- Wearable consumer electronics
- AR/VR components & equipment
- Automotive (focus on EV developments)
- Precision robotics
- MIM prototyping and bridge production
Production metals include:
- 17-4PH stainless steel
- 316 stainless steel
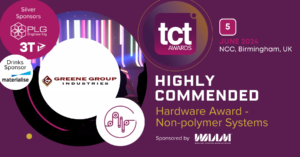
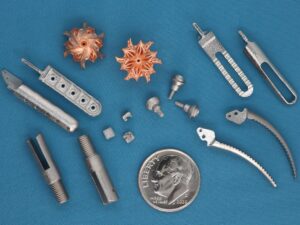
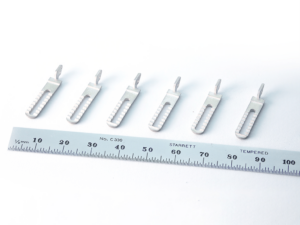
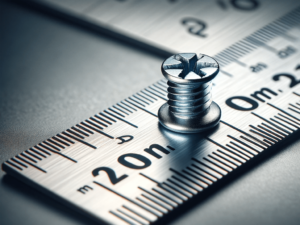